Good news! One of your most important customers just placed a huge order, and your shop foreman says you can save thousands if you just produce in bulk.
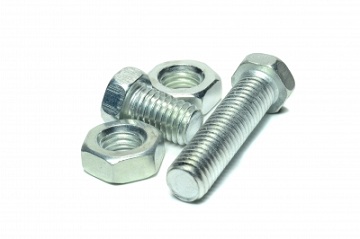
You’ll certainly take advantage of these opportunities, but with an increase in volume comes a new set of challenges, so it’s time to learn more about high volume production machining.
Advantages of high-volume
High volume production machining, simply put, employs methods for producing more parts at a faster pace. This will reduce unit costs and cycle times for the manufacturer, while pushing up deliveries to end users.
In many cases the production itself can be automated, freeing available workers to focus on tasks that require the attention of humans, while production rolls along. With solid, reliable machinery in place, production can even take place during non-working hours.
Disadvantages
Setting up high volume production machining comes with a steep price tag due to space requirements and the need for all equipment involved. Additionally, the ability to deliver customized items to your customer base will become limited.
At the same time, you need to inspect for quality. As molds and templates are used, they’ll likely wear out and lose some of the detail in the finished product. All of these drawbacks can be easily managed with a professional design , pre-production planning, maintenance and regular quality checks from skilled technicians. Like everything else, some production requests will work well, while others won’t. The critical component of high volume production comes from listening to and meeting customer needs.
As a full-service supplier of rapid prototype and precision production assemblies, PDS can deliver on any job from one-off highly complex parts for the medical industry to long runs for the transportation business. Contact us to learn more about what we can do for your business.