Corrosion. It’s the scourge of nearly every metal used in aerospace engineering. It strikes seemingly out of nowhere, inflicting damage that can remain silent for long periods of time.
Corrosion is frequently cosmetic and can ultimately prove debilitating. It can penetrate, pit and spread throughout aluminum, steel and magnesium alloys, feeding on oxygen in the air, the stress of external loads, improper heat treatment and ineffective heat treatments. All in all, it’s a critical concern in the aerospace industry.
Luckily, the increased attention to surface engineering has led to significant advances in corrosion protection. There are now a variety of tactics that expert finishers and painters can use to prevent corrosion and serve as effective surface treatment options for prototypes of aerospace parts and components.
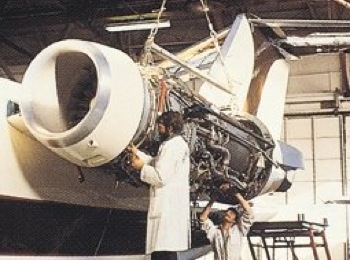
Coating
Soft alloys (those that are 200 HV or less) are particularly vulnerable to corrosion and steel rusts. Using a combination coating technique that includes a base coat along with a decorative topcoat can help prevent metals from breaking down.
The base coat adds hardness, structural support and corrosion protection, while the topcoat is primarily for aesthetic purposes.
Heat Treating
Heat treating is one of the most important and effective surface treatment options for prototypes of aerospace parts and components made of the alloys of aluminum, nickel and chromium. These metals, when not properly heat treated, often experience pitting.
During heat treating, the metals are heated and cooled in a controlled environment. While the shape of the part or component doesn’t change, its overall strength and ability to fight deterioration from oxidization, salt and even gasses, is greatly enhanced.
Conductive Coating
Conductive coating is primarily used to reduce electromagnetic or radio frequency interference related to electronic devices used in the aerospace industry. It also helps reduce corrosion on electronics by making them more resistant to hot and cold temperatures. The process involves coating the device with a durable, high purity nickel flake and is definitely worth the investment.
Fighting corrosion takes planning, the right surface treatment and expertise. You can get a fast quote from Product Development Solutions today and make sure your upcoming projects are corrosion free.