Sandpaper, fillers and solvents might be a thing of the past — at least when it comes to finishing fused deposition modeling (FDM).
FDM technology allows manufacturers to quickly and inexpensively create parts, patterns and tools. Bead blasting, a simple finishing process, not only takes a fraction of the time of sandpaper, fillers and solvents, but it also costs a whole lot less.
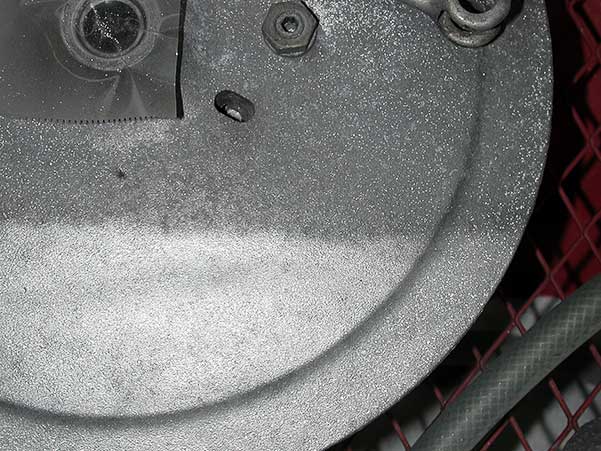
Bead blasting has quickly become a standard prototype and production service, and it’s easy to see why:
- The plastic beads are made from finely ground, recycled and reground thermoplastics
- Plastic beads last much longer than glass beads
- Beads are versatile and come in abrasiveness ranging from mild to ultra-harsh
But most importantly, it provides the smoothest finish. Here’s how it works:
Step One: Prepare the Model
Once the support structures are removed, masking tape is attached to areas of the model that don’t need to be finished. This includes sharp edges, parting surfaces and corners that might become rounded if blasted.
Step Two: Load the Bead Blaster
Once the model is prepared, the bead blaster needs to be loaded and fired up. Because bead blast comes in a variety of sizes and abrasiveness, it’s important to know exactly what type of finish is desired. The pressure setting should be set at a level that does not exceed 100 psi — too much pressure will create small holes, or divots, in the model.
Step Three: Bead Blast the Model
Afterwards, the spray gun is posited at an angle of about 60 degrees and will begin to lightly cover the part. The manufacturer will make sure to move the gun using a continuous sweeping motion, so the part is finished evenly. Better results are achieved by making several light passes over every surface rather than focusing on one area at a time.
Once the bead blasting is complete, the part will be rinsed and ready to use.
Bead blasting is changing prototype and production services for the better. You can find out how much you’ll save in both time and money by requesting a fast quote from PDS today.