It has long been one of the most difficult machining tasks in the industry. Its challenges include increased cutting forces and heat, uneven chip load and a lack of space for chip evacuation. This is the process of machining slots, which is a process that is far from easy.
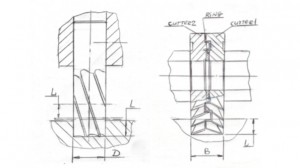
Fortunately, machinists have been studying the science of machining slots for as long as there have been milling machines. They’ve developed new techniques that involve diamond-cutting tools, regulation rings and attention to detail. The entire technical outline of the process is available, but the shorthand version is summarized below:
1. Machining precision slots require that an exact diameter DXL cutting tool be used. This allows for equal force to be maintained against each end of the gantry, improving the chance for an accurate cut. In addition, the length of the cutting tool needs to be two to three times the length of the milling machine.
As with any project that involves the process of machining slots, wear is inevitable. To obtain the most precise cut possible, use a “rest part” (which is standard on DXL cutting tools) to grind the butt-end teeth all the way to the bottom of the part.
2. Using a regulation ring allows for the cutting of any precision slot. Setting the ring between two disk milling cutters will compensate for wear and make the size of the tool smaller. Making the ring larger takes wear into account and allows the part to be ground into a precise size.
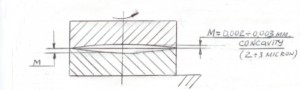
3. A diamond-plated cutter in addition to a circular, tilting or rotary table allows for the use of precision turning rather than scraping. This is the most efficient way to improve the process of machining slots.
Following these three setup steps can result in a more precise and efficient cut. More information about how to improve the process of machining slots with precision is available. Contact Product Development Solutions today for more information.