CNC machining runs from instructions delivered by computer software — this is the brain of the machine. The dirty work is performed by the tools actually carving, cutting and making the grooves in the material. Completing this job requires the skill and knowledge of an experienced tool designer who understands the detail needed for each part produced. Below are some basic tool design principles to keep in mind when designing a part.
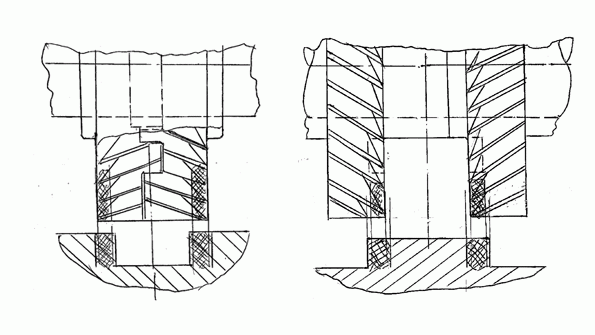
Know and understand these basic tool design principles
-
First off, the allowance for a cutting tool must be located within the allowance for a hole or groove. It must also be less than the allowance for holes or cutters.
-
Make a habit of sketching the locations of these two allowances. This will render an accurate image of the design and help you avoid mistakes.
-
To take advantage of the full material of the cutting tool, fix a maximum allowance for the tool. This will be less than the maximum allowance for the hole or groove mentioned above.
-
Finally, if the diameter of the cutting tool reaches the minimum of the cutting tool allowance, it should be removed from the machining operation. Machining must always be performed under controls. That’s what precision is all about.
A few more basic rules
The material used for cutting tools must be harder than the material you plan to cut, and it needs to withstand the heat generated from the job. Don’t forget to examine the angle of the cutting face, so the tool can do its job without dragging on the work piece’s surface.
The more you know about proper implementation of cutting tools, the longer those tools will perform reliably within the machine.
Product Development Solutions offers up concept-to-delivery consultation with every client. Our prototype and production service includes CNC machining expertise across many industries. Put your new product design on a path toward reality by getting a fast quote from our experts.